The automotive industry’s shift in interest toward Electric Vehicles is a source of enormous hope for the planet. EVs are getting steady support from governments and leading automakers and growing consumer interest is propelling the market growth.
The EV market value stood at $163.01 billion in 2020. It is projected to reach $823.75 billion by 2030!
The EV market has made great strides and it is estimated that these cars will seize one-third of the market by 2025. The top 29 OEMs plan to invest more than $300 billion over the next 10 years to further EV production with 400 new models hitting the market by 2025.
We can expect to see internal combustion engines (ICEs) replaced with zero-emission vehicles and move from the ICE age (pun intended) to the new, modern EV age.
The significant growth of EVs presents major opportunities. However, to capitalize on these opportunities and move on the path to profitability, OEMs need to navigate certain challenges. This is because, from component validation to on-road certification, the EV lifecycle is anything but simple.
The Complexity of the EV Landscape
The EV ecosystem, just like any automotive ecosystem, is a complex mix of OEMs, component suppliers, and startups. Despite regulations and government backing, OEMs are not yet making profits on the sale of EVs. These vehicles often cost $12,000 more to produce as compared to other ICE vehicles. Recouping those costs is often a struggle with carmakers with battery costs being one of the single big contributors.
Along with this, managing the whole vehicle program, infrastructure, validation stages, and design matrix verification at the enterprise level bring in a whole new level of complexity. Some of the other complexities involved are:
- Managing remote operations for testbeds, utilities, test data, and manpower
- Ensuring the data quality and certainty when recorded from the system
- Fast, efficient, automated, and reliable report preparation for weekly, monthly, and yearly audits for testbed maintenance
- Managing data, test plan, maintenance schedule, testbed slots, etc. in a single platform
- Identifying the field scenario for Lab-level test execution
- Making real-time models using fleet data and on-road test data
- Validating the components in the lab environment by stimulating field level scenarios
- Managing concurrent vehicle programs, DVP, complex development process, and growing requirements efficiently
- Establishing best practices and methods to manage large amounts of fleet data interface with analytics tools
- Identifying the most efficient and effective ways to record and manage field testing scenarios and field failure scenarios judiciously
Moving to the V-model of development solves these challenges and accelerates the industry toward profitability from both product and business-model perspectives.
What is the V-model?
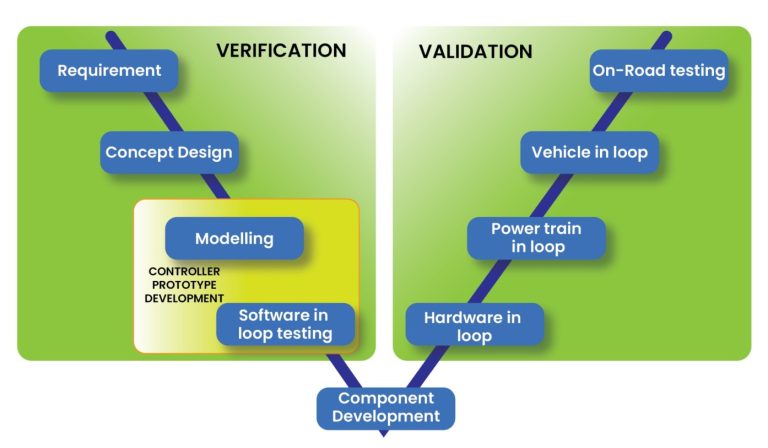
Since automotive development of EVs must adhere to regulatory standards such as ISO 26262 and ASPICE to minimize the risk of failure. It is essential to establish standard development procedures for positive outcomes.
The V-model is emerging as one of the widely used development processes in the automotive industry. This model splits the development process into two parts – Verification and Validation.
The left arm of the V consists of the Verification process consisting of requirement analysis, function design, and software development. The right arm of the V makes up the Validation process and focuses exclusively on the verification and validation activities followed by the release.
The V-model is hyper-focused on testing, especially the need for early test planning. Each part of this model aligns with the ASPICE standard and results in creating a clearly defined life cycle.
Several complex engineering products are now developed using the V-model since it efficiently helps enterprises manage deadlines as well as costs comfortably and conveniently.
The V-model Process Consists of:
- Requirements Engineering: Clearly defining the task/s that the automotive function/feature will perform and how.
- System Design and Development: Design and development of the function/feature according to the requirement. Functionalities are designed and tested using the model-based development environment to fix bugs early in the development cycle.
- Software development: Developing the software piece according to the model.
- Software Integration and Function/Feature Integration: Combining all the software modules during the software integration phase and checking the interactions between them while testing the impact of legacy code and other software modules. This phase is followed by function calibration where software parameters are further fine-tuned to drive top field performance
Technological disruptions and budget overruns are compelling OEMs, suppliers, and startups to migrate towards the V-cycle of development, connected data, and data-driven decision-making to accelerate time to market while ensuring quality deliverables.
The vehicle validation process involves multiple functional groups working and collaborating. As such transforming the classical validation process into data-driven engineering can help teams build efficient systems with lower time.
Leveraging a comprehensive integration platform to drive the V-model of development enables faster and more reliable decision-making by delivering the capability to combine data from different teams.
Power Your V-model with iASYS
With a legacy of the building of complex mechatronic systems and data management solutions, iASYS has the perfect product offering to help organizations adopt and use the V-model.
Our Road to Rig model allows the EV ecosystem to log failure situations, manage them with a unique identity, analyze the massive volume of data, and re-use the knowledge to improve existing DVP, FMEA, and replicate the same scenario in a powertrain rig.
Manage data and analysis needs for control validations
Our Distributed Brix platform is based on Spark for distributing analytics and using graph databases to produce semantically rich data. The platform allows for smooth transfers of large data volumes across various telematics analysis tools.
The platform lays the groundwork for MBD (Model-Based Development), as well as AI/ML-enabled physical model characterization and real-time plant simulations for control validations
Reduce costs and improve development time
The Orbit-EV platform addresses the challenges and needs of the OEMs, component suppliers, and startups. This platform supports the validation of all powertrain components-motor, motor controller, battery management system, battery, and battery chargers.
The platform supports interfaces to test critical components for field scenario simulation inside the rigs such as environment simulators, battery simulators, battery-charge discharge controllers, inverter simulators, CAN simulators, Motor simulators, Grid simulators, Robot-type driver simulators, and Dyno-based Road load simulators.
The platform enables the EV development community to generate scenarios throughout the validation life cycle. The platform also enables UUT testing from element level to vehicle level using different pre-built simulation packages
It allows the EV community to experiment and validate components with vehicle simulation. This virtual simulation also cuts costs and development time.
Augment battery testing capabilities
The Orbit BT platform enables the validation of BMS and batteries at the cell, module, and pack level. It allows the OEMs and component manufacturers support for thermal chambers, battery bi-directional charge-discharge controllers, and power analyzers.
It also offers battery testing procedures from USABC, ISO, UN, SAE & ARA and makes it easier to validate cases like the SOC estimation algorithm by allowing the user to validate cases at the component level.
Faster verification for optimized combinations
The Orbit EV platform is built to support the validation lifecycle at a powertrain level. Users can perform legislative, development, and durability trials using this platform while getting support for motor testing procedures for UN and ARAI.
The platform makes it easier for OEMs to verify design matrix combinations (Motor-Motor controller-Battery) of different vendors to finalize the best combination for their vehicles.
Validating functions like range estimation, the durability of the components, etc. at the vehicle level also become easier with the Orbit EV. It does so while supporting a wide range of power analyzers, Thermal chambers, Bi-directional DC power supplies (battery simulators), and interfaces to data-based models and physics-based models for simulations.
Ease of vehicle level validation trials
OEMs can simplify their vehicle level validation trials using the Orbit X platform. With provisions for test procedures from SAE, UN & ARIA, this platform provides support for power analyzers and DC power suppliers as well. It also supports Support for existing vehicle legislative cycles like IDC, WLTC, WMTC, etc. and test execution with Robotic Driver for durability trials.
In conclusion
Using the comprehensive Road to Rig solution, OEMs can manage a high amount of engineering data, growing complexities in products, and concurrent and connected development processes. This solution makes the validation cycle faster and more agile and allows for product building the PVM way.
Market demands have become more dynamic, customer needs are continuously evolving, regulations keep changing, and technological disruptions and budget overruns are common. Moving to a V-model helps EV companies manage deadlines and costs more effectively and efficiently.
The V-model makes the development process more connected. It ties data to decision-making and drives competitive differentiation by improving deliverable quality. Consistent data quality, test success, and a consequent lower time-to-market then become easily achievable goals.
Market demands have become more dynamic, customer needs are continuously evolving, regulations keep changing, and technological disruptions and budget overruns are common. Moving to a V-model helps EV companies manage deadlines and costs more effectively and efficiently.
The V-model makes the development process more connected. It ties data to decision-making and drives competitive differentiation by improving deliverable quality. Consistent data quality, test success, and a consequent lower time-to-market then become easily achievable goals.