Room for error in automotive production is inexcusable. The mistake of letting a flawed, subpar product stand the test of time can result in recalls and affect consumer trust and loyalty. In fact, even minor issues in the product design and development processes can spell disaster down the line, leading to millions of dollars in lost revenue and a significant drop in market share.
That’s why it’s more important than ever to drive processes that ensure all products meet exacting standards before their delivery to the customer. And one facet that serves to alleviate some of the headaches that come with ensuring product quality is the product validation and verification process.
What is Product Validation Management (PVM)?
PVM’s description can take a myriad of forms; however, the underlying principle of maintaining constant vigilance over product quality remains the same.
When speaking strictly for the automotive sector, the testing scenarios are endless and span the spectrum from minor tweaks on the component level to significant overhauls to the product’s design.
As such, it isn’t possible to run every test scenario in the physical world – making the need for a digital twin all the more essential. The digital twin of a physical product serves as an ideal simulation of the product’s components, design, and functionality — a capability that makes efficient validation testing a reality.
Nevertheless, to create a digital twin, we require data from physical testing. PVM entails using and unifying simulated and physical test result data to evaluate the product across the validation lifecycle.
In other words, PVM helps quantify the quality of the product during every stage of product development and allows manufacturers to carefully track the performance of design modifications and engineering throughout the process.
Such an approach drives the otherwise highly complicated, time-consuming, and error-prone process of validating product performance and quality in the real world.
Why Product Validation Management Essential for Automotive Companies?
The CASE (Connected, Autonomous, Shared, Electric) revolution is already well underway, and it’s creating a near-insurmountable list of challenges of product validation for companies that are still to get on with such fast-paced innovation.
The sheer interconnectedness of the latest vehicles – with their advanced electronics and cutting-edge components – renders them incredibly complex.
That apart, the industry is highly regulated as the stakes are high. More than 40% cost of the vehicle development program goes into product validation. However, physical tests take time and are time-consuming and costly.
Before getting to production, automakers must validate the performance of their designs in the digital world. After all, it’s impossible to anticipate every aspect of a vehicle’s functionality.
Besides this, advanced powertrains, sensors, safety systems, etc., are more sensitive than ever to changes in design. That’s due to the tight integration of proprietary technologies, which makes any malfunction in the automotive assembly process all the more catastrophic.
However, to accommodate this “tight integration,” stakeholders must access engineering data collected across every step of a vehicle’s life cycle – such as vehicle data, field data, and lab data. This, in turn, means that a holistic approach must be employed and that this data should be checked against real-world performance to prevent any discrepancies from arising.
But, in reality, this data is never unified, thus, plaguing both the upstream and downstream. Fragmented operations create disparate engineering data, which isn’t brought under a common umbrella. Hence, there’s no way to test the assumptions or get all stakeholders to validate the design.
Indeed, these challenges highlight the importance of PVM and its role in alleviating some of the pains of operating in a more complex manufacturing environment.
Product Validation Management – The Foundation of Digital Transformation
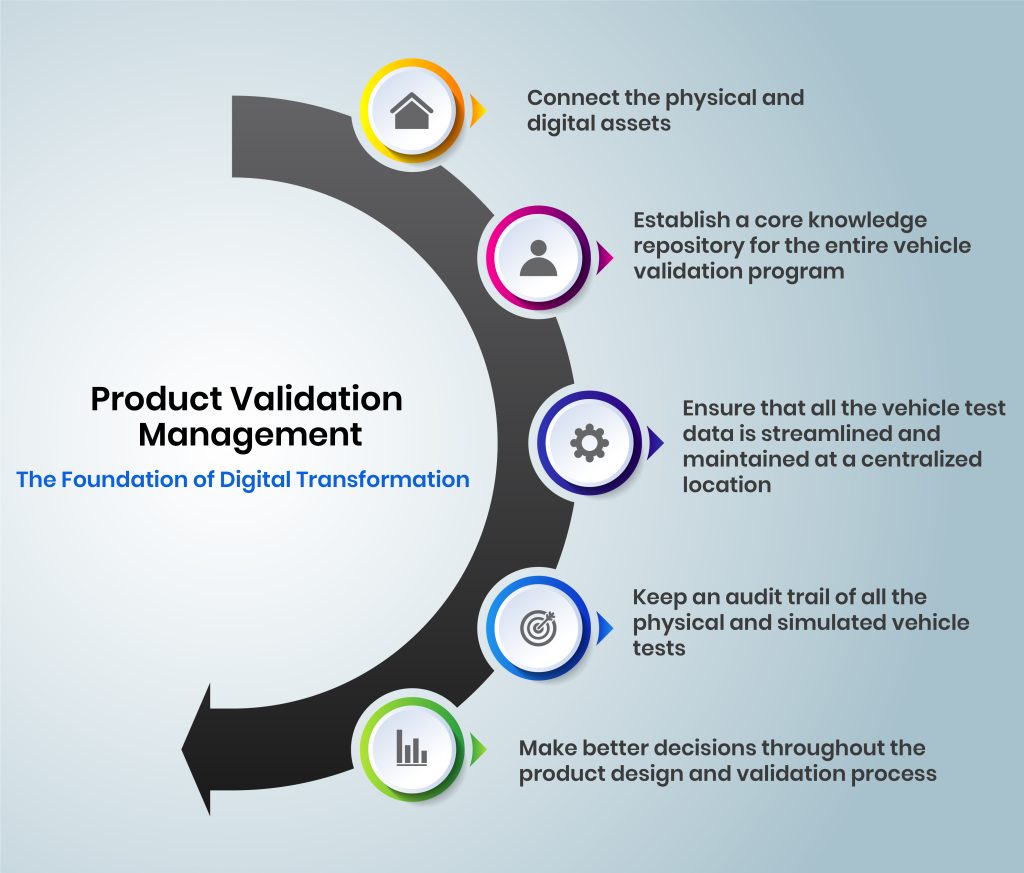
Product Validation Management sets the foundation of digital transformation for automotive companies. It helps in the digitization of the product design process, including conceptualization, design, and validation, before the vehicle actually gets into the production process.
With Product Validation Management, organizations can
- Connect the physical and digital assets
- Establish a core knowledge repository for the entire vehicle validation program
- Ensure that all the vehicle test data is streamlined and maintained at a centralized location
- Keep an audit trail of all the physical and simulated vehicle tests
- Make more informed decisions at every stage of product design and validation
With this, companies can achieve faster time to market, dramatic reduction in product development costs, and high quality.
How Does PVM Help Drive the Automotive Companies?
Over 90% of all the new products released every year fail to capitalize on their full market potential. That’s because they require “the perfect formula of innovation, perspiration, calculation, and luck” to succeed, writes Marc Emmer for Inc.
And while innovation is undoubtedly critical, having the right resources to ensure the product is correctly designed, engineered, and manufactured is equally essential. That’s precisely where PVM serves to safeguard a company’s bottom line by ensuring everything runs as it should. Here’s how:
● Standardization of Different Engineering Test and Validation Data
As elucidated above, massive heterogeneous engineering data with no common denominator make the design and development process particularly cumbersome.
By bringing together different engineering test and validation data with a common identifier (a standard format), PVM allows automotive companies to create a “golden standard” and map all engineering data points to it.
● Conversion of Test and Validation Data into Knowledge
The data collected across different engineering and test stages become actionable knowledge, leading to improved decision-making and a reduction in the number of defects at the end of the product development phase.
This further reduces development costs and time and complements the OEM-specific Validation plans. The result is a product that can be delivered with greater certainty.
● Using System-level Metadata for Cross-Functional Collaboration
This links back to the first advantage – the common format across different engineering data fields. This leads to first-class interoperability for all the stakeholders involved in the PVM process.
Such a metadata dictionary serves as a common repository for the data that’s being collected in the validation operation, ensuring all engineers, design, researchers, and test validation teams have access to the same information.
It also helps the downstream vendors understand their engineering data requirements to communicate their inputs effectively.
● Organized Data Storage for Reuse
Thanks to the metadata dictionary, the data collected in the PVM process is stored in a structured manner and can be easily accessed anytime by all the relevant stakeholders. This brings considerable benefits to the company’s bottom line, as it can reuse this data to save costs during various stages of development.
For instance, the same data might come in handy during the validation of the existing product design and the development of future iterations.
● Getting Everyone Onboard
Validation designer, validation engineer, test planner, test engineer, facility engineer – the list of stakeholders who must play a part in the PVM process is vast.
However, without a common approach for communication and collaboration, it’s impossible to effectively make use of the valuable data gathered during production.
That’s where PVM comes in to act as a unifying force. With its ability to bring together the different stakeholders, PVM facilitates faster decision-making, improved collaboration, and stronger relationships across the entire operations chain.
This serves to enhance interoperability, reduce production defects, and expedite faster time-to-market.
Realize All the Benefits of PVM with the BRIX Platform
With automotive companies adopting a more holistic approach to product development and manufacturing, there’s a growing need for better data management and sharing across the operation chain.
The BRIX platform by iASYS is designed to fill this gap by acting as a unifying hub for data, which underpins its ability to bring everyone under one roof.
Drop us a line to find out more. We’ll help you plan and track a flawless product life cycle.